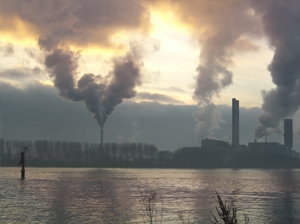
Durante su tiempo de vida, un equipo de fabricación –por ejemplo, un equipo de fabricación de componentes de automóvil– atraviesa varias etapas, comenzando con su incorporación inicial en la línea de producción, operación y mantenimiento hasta su fin de uso y desmantelamiento. En ese camino hay un número de situaciones que encarecen el proceso, como paradas de la máquina, o incluso de todo el sistema de producción, y el desmantelamiento del equipo. Esto tiene como consecuencia retrasos en la producción, mayores costes y desechos de equipos industriales.
El proyecto europeo ReBorn, en el que participa el Departamento de Ingeniería Química Industrial y del Medio Ambiente de la Escuela Técnica Superior de Ingenieros Industriales de la Universidad Politécnica de Madrid (UPM), busca revolucionar las actuales estrategias industriales de producción incrementando el índice de reutilización de los equipos industriales, favoreciendo la sostenibilidad del sistema y disminuyendo la inversión.
En la actualidad, el nivel de reutilización de los equipos es menor al 25 % en casi 9 de cada 10 fábricas, mientras que una media del 50% de los equipos podrían reutilizarse, según se extrae de una reciente encuesta realizada por el consorcio del proyecto ReBorn entre la industria manufacturera europea.
El objetivo de ReBorn es “lograr prototipos que se puedan integrar de forma modular en distintas configuraciones de fabricación para conseguir el 100% de reutilización de los equipos, lo que daría solución a la escasa capacidad de reutilización actual”, explica la catedrática de la UPM Alicia Larena. Para ello, los investigadores basan su trabajo en los conceptos de autoconciencia y autointeligencia, es decir, de la capacidad de autoprogramación de componentes y equipos que configuran un proceso de fabricación dado, y de la capacidad de recopilación, almacenamiento y análisis de datos de la historia del proceso; en definitiva, en el desarrollo de equipos que tengan conocimiento de todo el proceso de producción.
“Se trata de crear sistemas flexibles y modulares que se compongan de componentes estándar y que permitan una fácil re-configuración y extensión mecánicas, de manera que se aumenta la rapidez de reacción al cambio de las demandas de producción y se reducen los tiempos”, asegura la investigadora.
El papel de la UPM en la investigación es aunar el establecimiento de una metodología basada en el uso de sistemas modulares formados por componentes reconvertibles, hardwares reconfigurables y softwares reprogramables.
“Imagina que el equipo de una línea de producción no sólo cumple una tarea aislada, sino que actúa como un proceso dinámico siendo parte especializada de una orquesta de partes inteligentes. Este tipo de sistemas de producción flexible (plug & produce), es decir, con capacidad propia de autoadaptación, está compuesto de componentes inteligentes capaces de comunicarse entre sí en una red con auto-conciencia de su estado y de su función, así como de su evolución en el tiempo”, explica Alicia Larena.
El proyecto cuenta con un total de 18 participantes entre universidades, empresas y centros de investigación de diferentes países de la Unión Europea. Su importancia radica en que sus resultados podrán aplicarse a todo el tejido industrial-empresarial, con especial énfasis en ventajas económicas competitivas para el sector manufacturero. Asimismo, se pretende contribuir a fomentar una mayor conciencia social sobre el uso eficiente y ecológicamente sostenible de los recursos para cumplir con los desafíos del cambio climático global y la escasez de recursos.