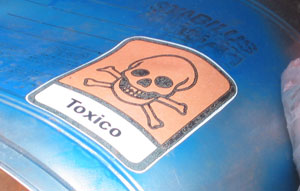
El grupo de investigación "Análisis y diseño de procesos con fluidos supercríticos", perteneciente al Departamento de Ingeniería Química y Tecnología de Alimentos de la Facultad de Ciencias de la Universidad de Cádiz (UCA), se centra en el tratamiento de vertidos industriales tóxicos y con altas concentraciones de materia orgánica, como aceites, disolventes o hidrocarburos; residuos que hacen pasar por una tubería a alta presión, donde además se calientan hasta 400 ºC. En otra línea tubular, se añade el oxidante. Cuando ambas tuberías –las de residuos y la del oxidante- alcanzan las condiciones de presión y temperatura, van a parar a un reactor de escasas pulgadas de diámetro y varios metros de longitud, donde se produce una oxidación completa de los compuestos contaminantes, depurando por completo el agua resultante.
"Su pureza es adecuada para verterla a un cauce público o directamente al mar", señala Juan Ramón Portela, uno de los investigadores participantes en el proyecto, y añade que la utilización de este medio de reacción supone una prometedora opción debido a las especiales propiedades que posee y las grandes ventajas que su utilización conlleva frente a otros métodos más convencionales.
Estos beneficios guardan relación con su sostenibilidad ambiental, ya que esta técnica no genera compuestos tóxicos, como ocurre en otros métodos tradicionales de descontaminación, como la incineración. La oxidación en agua supercrítica (OASC) se denomina "combustión fría", ya que trabaja con temperaturas inferiores a la combustión convencional (400-600 grados centígrados, frente a los 900-1.200 de la incineración). A la nula toxicidad, la baja temperatura de la OASC se suma su efectividad. "Los compuestos orgánicos y el oxígeno están en íntimo contacto, por lo que el proceso de oxidación tiene lugar sin limitaciones, lo que aumenta considerablemente la velocidad efectiva de reacción", explica Portela.
La industria, una meta cercana
Una vez conseguida la descontaminación en un reactor piloto, los investigadores de la UCA trabajan ahora, en colaboración con investigadores de la Universidad de Sevilla, en desarrollar la técnica a escala industrial en el marco de un proyecto de excelencia, que la Consejería de Economía, Innovación y Ciencia ha financiado con 388.208 euros.
La transferencia del método a la industria pasa por solventar algunas dificultades que, aunque se pueden controlar en el laboratorio, aparecen en la aplicación real como son el arranque y control de la instalación, la gestión del calor que se genera en la reacción o la disminución de la presión de los efluentes del proceso.
Por un lado, en los ensayos que acometen los investigadores resulta relativamente fácil que el agua alcance elevadas temperaturas, pero, en la industria, se necesita mucha potencia para que grandes volúmenes del líquido se calienten. Para solucionar este inconveniente, los expertos no calientan el agua residual mientras circula por el sistema, sino que le aplican calor mientras la mantienen retenida en las conducciones. "De esta forma, aunque se aumenta el tiempo de calentamiento, se disminuye la potencia eléctrica que hay que aplicar", resume Portela.
En cuanto al obstáculo de la elevada energía liberada, los investigadores han diseñado un sistema para aplicar corrientes de agua fría en varios puntos del reactor. Asimismo, también es posible repartir la cantidad de oxidante a añadir en diferentes zonas del reactor.
En el caso de la descompresión de los efluentes que se originan en el proceso, los investigadores están evaluando la viabilidad de simplificar la operación mediante un nuevo sistema de tuberías de gran longitud que hacen disminuir la presión del agua que circula por ellas.
Los expertos persiguen superar estos obstáculos para optimizar el aprovechamiento de la energía liberada en el proceso, con el fin de mejorar su viabilidad técnica y económica a escala industrial.